These approaches have encountered problems, including porosity of the cladding, uneven cladding thickness, dilution of the cladding alloy due to the big heat enter required, and distortion of the workpiece by the excessive heat enter. Laser cladding has reduced these issues and produced cladding layers with good uniformity, good dimensional management, and minimal dilution of the cladding alloy. gives a survey of a cladding gear. If the incoming strips must be heated so as to lower the power of materials, this needs to be accomplished as close as possible to the rolling hole and in a protective environment so as to avoid oxidation of the cleaned and roughened surfaces. We provide excessive-high quality decorative products that improve any house and interior.
The effect of thermal conductivity degradation on the efficiency of the fuel is illustrated in Fig. 1 . This reveals the outcomes of calculations during which the facility in a rod is artificially held at a constant stage.
Its industrial identify is Zircaloy, or Zry for brief. Zry is available in two varieties, Zry-2 and Zry-four. These two differ by minor changes within the concentrations of the transition metals (Zry-four has no nickel). PWRs use Zry-4 whereas BWRs employ Zry-2 as cladding and both Zry-2 or Zry-4 for the duct or channel holding the gas-factor bundle.
The soften layer is kind of skinny; for example, when cladding an aluminum alloy it is about 0.5–fourμm (Kreye 1985, 1997 ). The dilution of the molten zones leads to plane or corrugated interfaces. During mechanical decladding, the gas assemblies are chopped and the fuel core is leached with nitric acid, leaving behind the undissolved cladding material for disposal as a strong waste.
In one, a second internal-surface liner of ordinary Zry is extruded on the sponge zirconium liner so as to restore corrosion resistance. In other modifications, the sponge zirconium is alloyed with iron or tin to enhance oxidation resistance without affecting the softness that provides immunity from PCI. Standard Zry is sufficiently onerous to be vulnerable to stress-corrosion cracking (SCC) when the pellet–cladding gap closes and the swelling gasoline generates substantial tensile hoop stresses within the cladding. In the presence of an aggressive fission product (iodine is most often cited), a brittle crack can be initiated and penetrate the cladding wall.
The course of is commonly used to create a protective coating for elevated performance, as well as restore damaged or worn surfaces. Laser cladding permits prolonged life of apparatus and machinery by which parts are uncovered to corrosion, put on or influence. For instance, the construction tools industry applies this expertise to their products to increase put on resistance and hold equipment in service longer. A excessive-energy laser is used as the warmth source in laser cladding. During the method, a surface layer is created by means of melting and the simultaneous utility of virtually any given materials.
The buildup of those may be suppressed by adding hydrogen within the coolant water. Dissolved hydrogen focus in PWR coolant is maintained at a stage of two.2–four.5 ppm with a view to enhancing recombination with oxygen radicals formed by radiolysis. The PHWR coolant does not include boric acid and deuterium is added in place of hydrogen.
Hydrogen addition in boiling water situations just isn't very effective due to the segregation of hydrogen within the steam section. The interaction that fuel cladding tubes expertise as a result of fission products on the inside floor is stress corrosion cracking (SCC). Iodine, caesium, and cadmium are some of the fission products which contribute strongly to the SCC course of. Due to the mixed effects of thermal expansion of fuel pellets, gas swelling due to fission gas launch, and the coolant strain on the outer floor of gas tubes, cladding tubes collapse on the fuel pellets.

Interior PVCu Cladding
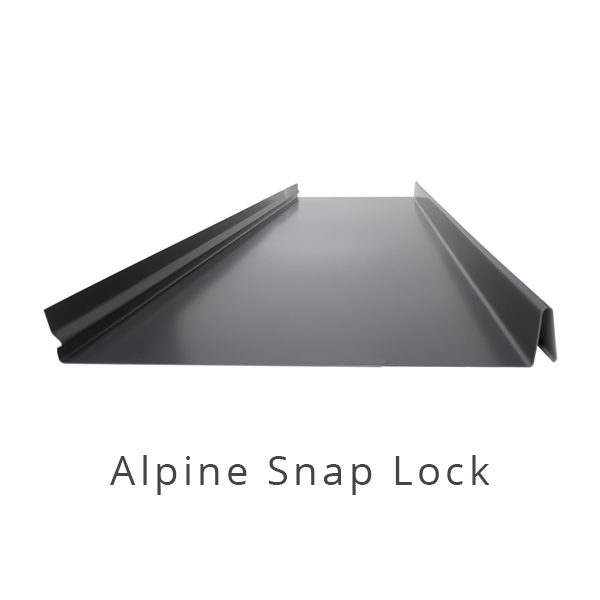
Once the pellet/clad gap is closed, any change in pellet dimensions causes stress within the cladding and the synergy between the stress and the corroding medium induces the SCC process. In order to forestall or reduce pellet/clad interactions, both mechanical and chemical, a coating of graphite powder is utilized on the inside floor of cladding tubes.
The soften layer is kind of skinny; for example, when cladding an aluminum alloy it is about zero.5–fourμm (Kreye 1985, 1997 ). The dilution of the molten zones leads to plane or corrugated interfaces. During mechanical decladding, the fuel assemblies are chopped and the gasoline core is leached with nitric acid, forsaking the undissolved cladding materials for disposal as a solid waste.
Our vast vary of products includes PVC wall panels, outdoors wall cladding, waterproof flooring as an alternative to laminate or LVT, water-resistant bathe and toilet panels and rather more. These embody cladding, small steel pins coupled with a ceramic mass, half-pipes and SiC tiles, as well as varied forms of coatings, including thermal spray coatings. Its attribute feature is the sash bar down the center of the window and black (similar to RAL 9005) steel cladding coverings on the window and flashing which matches conventional buildings. The Independent Expert Advisory Panel also advised the department to establish a research challenge to test and enhance the proof out there on the behaviour of a range of non-ACM supplies used in cladding systems when subjected to fireplace.
The transition metals iron and chromium appear in the microstructure as precipitates of the intermetallic compounds Zr 2 (Ni,Fe) and Zr(Cr,Fe) 2 . These minor alloying parts enhance corrosion resistance to an extent dependent on the dimensions of the precipitates. Laser cladding has been utilized to hardening of steam generator turbine blades and reached pilot manufacturing standing [four ]. The blades had a machined pocket, into which powdered cobalt-based metal (Stellite 6) was fed forward of the laser beam.
Joining happens continuously by native plastic deformation of the contact area (Ruge 1993 ) (see Fig. 1 ). Figure 6 . Schematic diagram displaying the mechanism of the oxidation process and the oxide movie construction on zircaloy. Figure 5 .
The oxidation course of and the nature of the oxide layer on a zirconium alloy sample are schematically illustrated in Fig. 6 . Cladding is an outer layer of both vertical or horizontal material, used to enhance the appearance, thermal insulation and the climate resistance of a constructing. Our cladding is on the market in quite a lot of sizes, types of timber and floor finishes.
The constants a and b are basic properties of the fabric and can be determined from standard laboratory experiments on fresh gas. In explosive welding, a compression force created by detonation of explosives is used to affix overlapping metallic sheets. The joining elements are arranged in direction of each other at an angle of 1–15°, depending on the fabric and methodology, and are ready with a layer of explosive on the highest. After ignition the joining areas are moved in opposition to one another at excessive velocity.
In PWRs the closure of the gap between the pellet and the clad takes about one full power 12 months whereas the hole is maintained for a longer interval in BWRs. Due to the collapsible clad design of PHWRs, contact between the pellet and the clad is established proper from the beginning of the lifetime of the gas element. Laser coating or laser cladding can be utilized to regionally functionalize metallic parts. In this process, an edge layer of typically 0.1 to 2 mm is applied to the component. The coating material employed is both powder or wire, or utilized upfront as a tape.
For the identical exterior loading, the stress produced in the cladding, either external from the coolant or internal from fission-product swelling of the gas, is reduced in proportion to the wall thickness. However, thick cladding is detrimental to neutron financial system, increases the quantity of the reactor core, raises fuel temperature, and costs more than skinny-walled tubing.
Wire-based mostly laser deposition welding is a cloth-environment friendly 3D printing process for the manufacturing of metallic parts.
Today, Zircaloy-2 and Zircaloy-4 are extensively used. Phase transformation of Zirconia is, nevertheless, of great concern.
In addition to metallurgical factors, water chemistry has a powerful influence on the corrosion course of in zirconium alloys. The control of water chemistry as required in several reactor techniques embrace suitable additions of lithium hydroxide, boric acid, hydrogen/deuterium, oxygen, iron, and zinc. In PWRs, boric acid is added to the coolant water for reactivity control. The pH of the coolant is adjusted by addition of lithium hydroxide which renders the coolant slightly alkaline, in order to reduce the corrosion charges of structural materials (stainless steels and Inconels) within the primary warmth transport circuit and thereby inhibit deposition of corrosion products on the gas cladding. Radiolysis of water produces oxidizing species which boosts oxidation rate of zirconium alloys in the radiation setting .
The transition metals iron and chromium appear in the microstructure as precipitates of the intermetallic compounds Zr 2 (Ni,Fe) and Zr(Cr,Fe) 2 . These minor alloying elements improve corrosion resistance to an extent dependent on the scale of the precipitates. Laser cladding has been utilized to hardening of steam generator turbine blades and reached pilot production status [four ]. The blades had a machined pocket, into which powdered cobalt-primarily based steel (Stellite 6) was fed ahead of the laser beam.
As a treatment, speedy cooling of the Zry ingot during fabrication (called beta quenching) produces a much finer intermetallic precipitate inhabitants. This distribution of the transition metals maintains the strength of the Zry but improves its corrosion resistance, probably by brief-circuiting cost-transport paths between the scale floor and the metallic–oxide interface. In order to eliminate waterside corrosion of cladding as a life-limiting process, modified Zircaloys have been developed. Under PWR water situations, decreasing the tin content of Zry to 1% and including a comparable concentration of niobium produces an alloy with a corrosion price several occasions decrease than that of the standard Zry. Modified low-tin alloys can be utilized both as a complete substitute for the Zry tube wall or as a skinny outer skin on normal Zry substrate tubing.
Cladding allows the majority of the half to be made with inexpensive materials, while offering the surface with fascinating properties related to the more expensive cladding material. Laser cladding has resulted in surfaces with very good finish, good homogeneity, and really low porosity. Common supplies used for cladding embrace carbides, iron-based alloys, nickel base alloys, and cobalt base alloys. Laser cladding is a course of by which a steel coating is applied onto the floor of a component utilizing a laser as the heat supply.

Non-aluminium composite materials Click This Link cladding
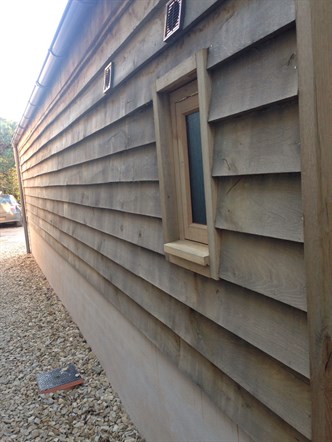
Today, Zircaloy-2 and Zircaloy-four are extensively used. Phase transformation of Zirconia is, however, of nice concern.
For the identical external loading, the stress produced within the cladding, both exterior from the coolant or inner from fission-product swelling of the fuel, is lowered in proportion to the wall thickness. However, thick cladding is detrimental to neutron economic system, increases the volume of the reactor core, raises gas temperature, and prices more than thin-walled tubing.
The compromise between these competing calls for has produced wall thicknesses of ∼0.9mm in BWRs and ∼zero.7mm in PWRs. Laser cladding usually includes overlaying a relatively inexpensive substrate materials with a costlier alloy that may increase the resistance of the half to wear or corrosion.
Zircaloys additionally endure from bad creep charges. In contrast to floor-layer welding, explosive welding causes no change in microstructure, and corrosion resistance of the layers just isn't affected (Pocalco 1987 ).
laser. The clad substrates confirmed improved oxidation characteristics compared with the original alloy. Conventional methods for cladding have employed tungsten-inert fuel welding, plasma spraying, and flame spraying.
tube. Energy, from fission, is generated approximately uniformly all through the fuel pellets. Heat is extracted at the rod floor by the coolant flow. The temperature at the hottest level, on the pellet centerline, is usually within the vary 800–one thousand °C, depending on the power level. The metallic cladding is an efficient conductor, so the temperature rise across the wall is only some tens of levels.
Cladding permits the bulk of the half to be made with cheap materials, whereas providing the surface with desirable properties related to the costlier cladding material. Laser cladding has resulted in surfaces with very good end, good homogeneity, and very low porosity. Common materials used for cladding embody carbides, iron-based mostly alloys, nickel base alloys, and cobalt base alloys. Laser cladding is a course of during which a steel coating is applied onto the floor of an element utilizing a laser as the heat source.
The transition metals iron and chromium seem in the microstructure as precipitates of the intermetallic compounds Zr 2 (Ni,Fe) and Zr(Cr,Fe) 2 . These minor alloying elements enhance corrosion resistance to an extent depending on the scale of the precipitates. Laser cladding has been utilized to hardening of steam generator turbine blades and reached pilot production standing [4 ]. The blades had a machined pocket, into which powdered cobalt-based mostly metal (Stellite 6) was fed ahead of the laser beam.